Mar 24, 2023 - 7 mins
Resins and additives: a leading offering for more sustainable coatings
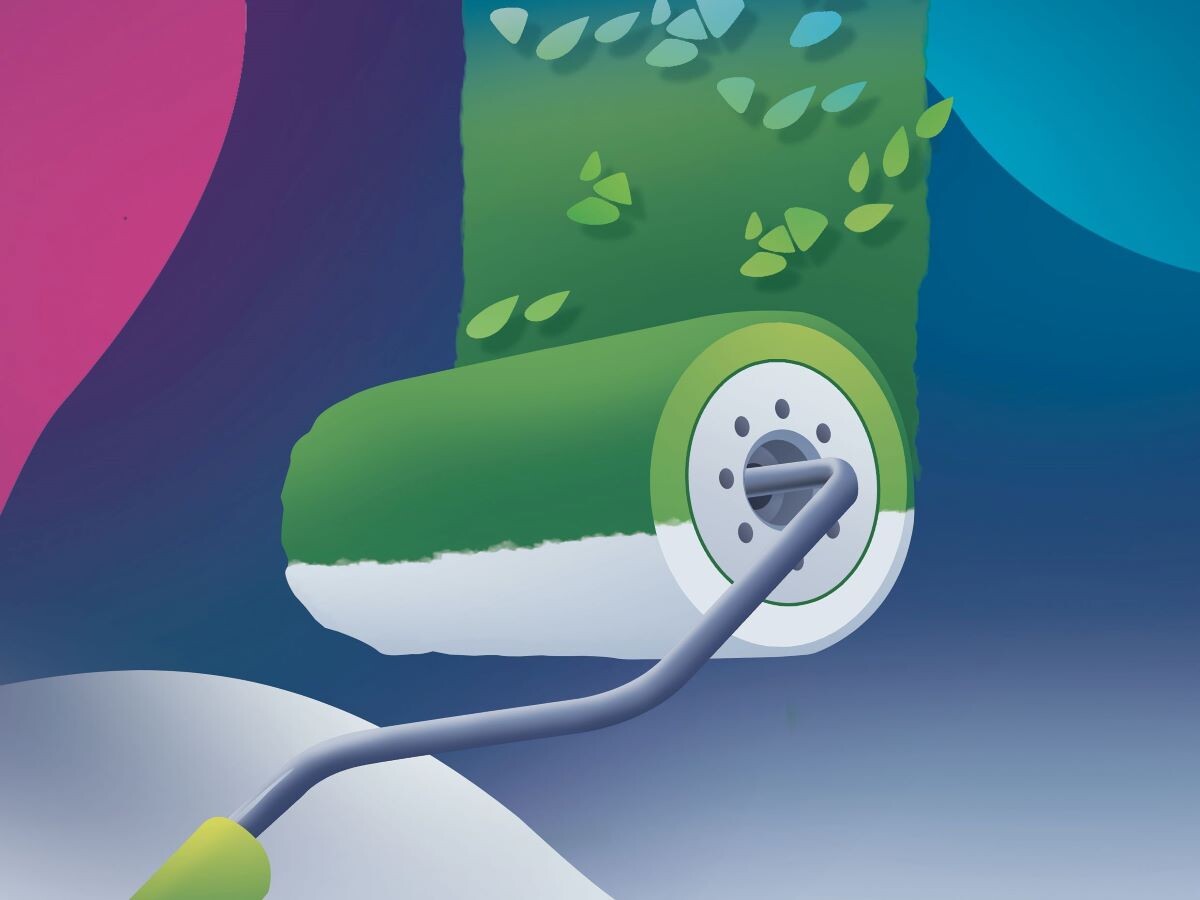
Interior decoration, boats, construction, automotive, touchscreens, packaging, industrial timber, metal infrastructure and more: the coating sector covers a huge range of applications and meets demanding and varied aesthetic, functional and regulatory specifications. Arkema is one of the world’s leading players: its vast portfolio of materials - resins and additives - provides manufacturers of paints, varnishes and lacquers with solutions that meet market expectations, increasingly driven by energy and climate challenges.
Our role is to support the transformation of the coating sector by focusing on four major aspects: phase out of hazardous substances, the quest for bio-sourced raw materials, development of more efficient and sustainable technologies and the evolution of application processes toward greater industrial and energy efficiency.
Our four main areas of improvement
Phasing out hazardous substances: staying one step ahead of regulations
Phasing out hazardous substances (HAPs*, heavy metals, volatile organic compounds, etc.) is a critical issue in the coating sector, driven by increasingly stringent regulations. An underlying trend that is driving Arkema’s entire Coatings offering: the Group anticipates the implementation of new standards to offer its customers, manufacturers of paints, varnishes or lacquers, a wide range of solutions that comply with the highest health and environmental standards, beyond regulatory requirements. Its proven expertise in solvent-free (aqueous, powder and UV-curable resins) and high-solid resins technologies also makes it one of the world’s leaders in reducing the use of volatile organic compounds in coatings.* Hazardous Air Pollutants
Bio-sourced solutions: for coatings with a lower carbon footprint
The search for alternative feedstocks based on renewable or partially recycled materials is one of the main areas of focus in Arkema’s policy for reducing the carbon footprint of coatings. In the context of decorative paints and lacquers, this has led to the Synaqua® range of alkyd resins, which have a high content of bio‑sourced materials: from 42% to 96% of total carbon, depending on grade, mainly from paper byproducts. For photocurable specialty coatings, Arkema offers UV Sarbio® resins, based on renewable raw materials. Synaqua® and Sarbio® products have been awarded the USDA* label, which certifies their bio‑sourced content.In the context of specialty additives (modifying the fluid behavior of formulations), the Group has proven reference products in this field, with the Crayvallac® ranges (80% based on castor oil derivatives) for marine paints and construction sealants, and the Coapur™ range, which will introduce new bio-renewable raw materials based thickeners for aqueous paints. In 2021, the Group also initiated a “mass balance” sourcing approach for its acrylics sector (see box opposite).
* US Department of Agriculture
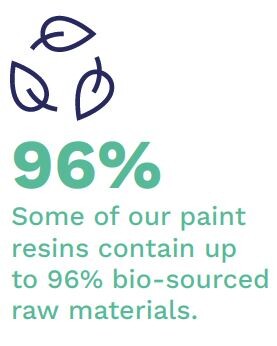
A unique combination of technologies geared toward sustainability
The Group is one of the few companies to have invested simultaneously in all four current coating technologies. For which it has world-renowned solutions aqueous resins, such as the Encor® Flex range and Kynar Aquatec® emulsion used for cool roofing applications ; high-solid resins, which are diluted in application (in the context of industrial coating); powder resins, increasingly used in hyper durable industrial coatings; and photocurable resins to achieve greater durability and a high-end coating finish. This unique combination enables the Group to provide more sustainable and innovative solutions in the most dynamic segments of the market.Application processes: a driving force for performance and energy efficiency
Its high-solid resins combine lower transport costs with better industrial efficiency during application; its powder resins, like Reafree® polyester resins, are characterized by their low baking temperatures. Finally, its photocurable resins represent a breakthrough technology for industrial coating with considerable time and energy savings compared to conventional processes.
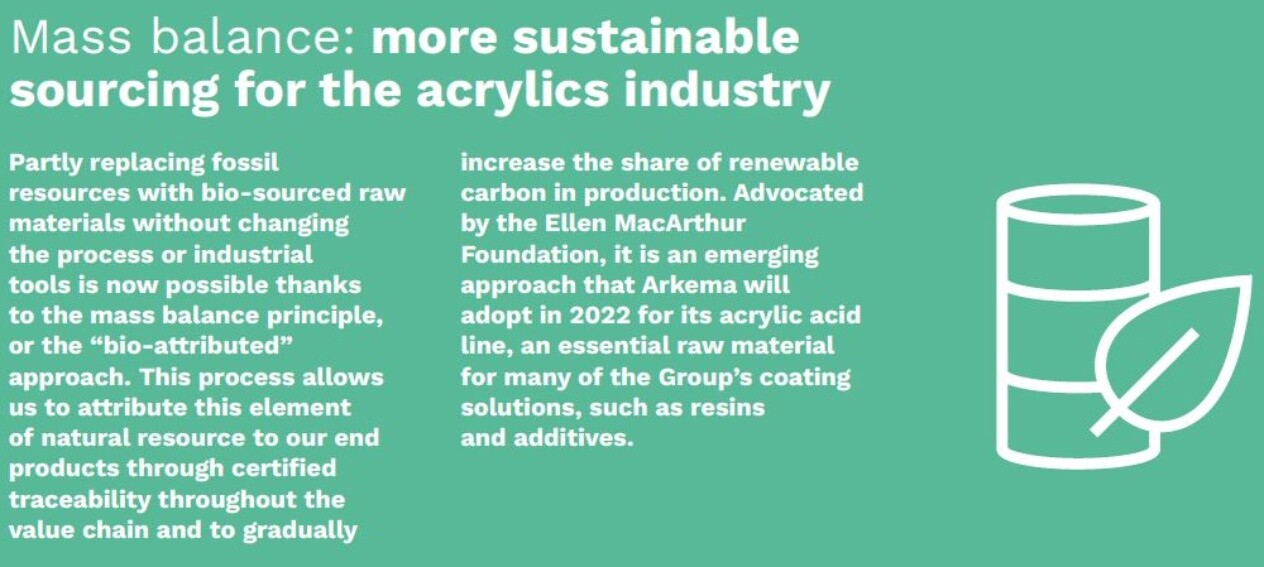
UV resins and powders: “zero solvent” on the rise
UV resins: saving time and space
Floors and furniture, automotive parts, packaging for cosmetics, modrn PVC flooring, consumer electronics: the specifications for coating (varnishes, paints and lacquers) need to be highly resistant and offer a high‑end finish. For all of these applications, Sartomer® UV resins are an established solution of choice, formulated and applied by means of a completely volatile organic compound-free process.These resins dry instantly under UV light (compared to several hours for more conventional coatings), resulting in significant savings in time, energy and space: a line of paint 100 meters long can be replaced by a machine a few meters long. A new technology for which Arkema is a global leader, with more than 300 products in its portfolio, truly functional “bricks” that enable manufacturers to meet their customers’expectations.
Powder resins: less is more
At the same time, in its range of Reafree® polyester powder resins, Arkema has another “zero solvent” solution that has been adopted by an increasing number of customers in the industrial coating sector.This technology does not require diluents for its application and therefore does not generate atmospheric emissions. In addition, it offers exceptional performance in terms of durability: with morethan 90 products, the Reafree® range is used in many applicationsranging from household appliances,such as refrigerators and washing machines, to metal garden benchesand a wide range of marine and industrial equipments.
Arkema is investing in R&D to develop these technologies of the future, as explained by Chris Miller, Head of R&D for the Coating Resins business unit: “Our global network of dedicated laboratories enables us to develop new solutions for innovative formulations that are less energy intensive. They provide ‘superdurability’ and can help companies across the value chain improve overall performance.”
Cool roofing: Kynar Aquatec® emulsion, the agent that protects white roofs
More roofs on large shopping centers and logistics warehouses, particularly in Europe, are adopting cool roofing to bring the temperature of buildings down during periods of warm weather. “In 2022, 400,000 m2 of additional roofs will be covered in France by our partner Cool Roof France”, announces Bertrand Dinelli, High-Performance Polymer European Market Manager at Arkema. Approximately 15% on the energy bill of buildings can be saved, thanks to the combination of a white aqueous paint and a transparent anti-UV overcoat of Kynar Aquatec® resin, which increases its ability to reflect solar radiation and protects it from mold and dirt for nearly 20 years. “Our coating also enables the roof to self-clean when it rains, much like an oilcloth, while providing a seal that prevents the release over time of residues from the undercoat”, emphasizes Bertrand Dinelli.
Government recognition
This solution has been approved since 2021 by the ATEE (French Energy Environment Technical Association), the body that manages energy saving certificates in France: a major step forward, which will enable developers to benefit from government grants to switch to cool roofs.This recognition could also be awarded in other European countries, such as Spain and Italy. Moreover, Arkema’s Encor® Flex acrylic emulsion, sold in the United States for roof coatings, is an undercoat that is perfectly tailored to use with Kynar Aquatec® emulsion.
See also
Back to all articles- Expertise articles
- Expertise articles
- Expertise articles