- Expertise articles
- Automotive
- Composites
- Construction and Building
- Lightweight materials & design
- Renewable Energies
- Sustainability
Dec 6, 2021 - 7mn
Elium® Resin: a breakthrough innovation in composite materials
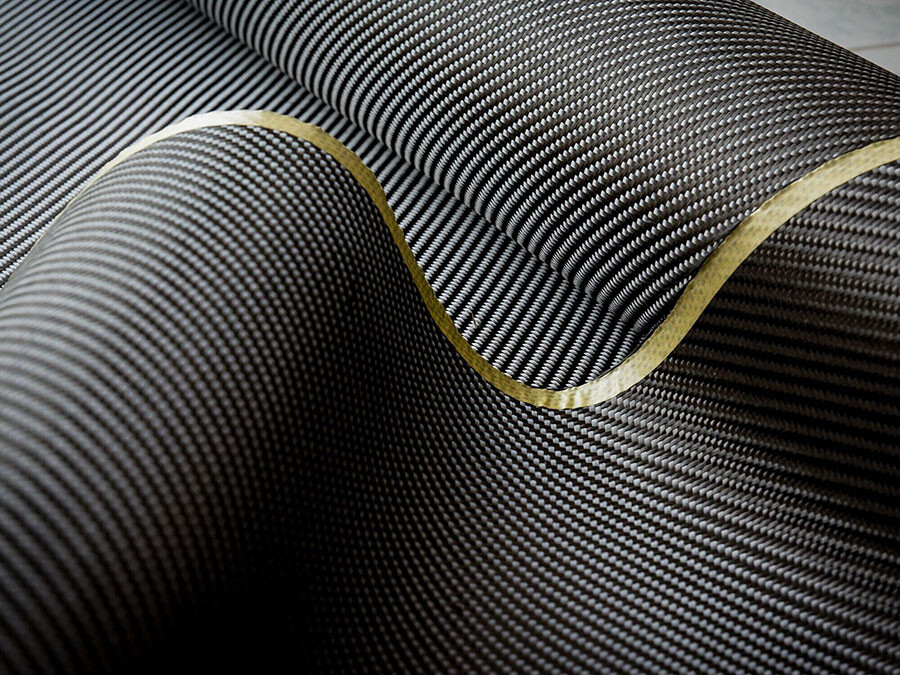
MEET…
GUILLAUME CLÉDAT, Elium® resin Business Development Director
With its Elium® thermoplastic resin, Arkema offers a unique solution for manufacturing composite parts using the same methods as those used for thermoset resin parts, but with the major advantages of recyclability, more energy efficient production and thermosetting possibilities. This could benefit a number of sectors, such as wind power, automotive, construction and sailing.
Why did you develop Elium® resin?
Guillaume Clédat – We wanted to make thermoplastic composite materials more accessible for our customers and easier to use. And that's what Elium® resin does. It's easy to use as it is liquid like other resins, which are currently very widely used, but with the advantage of being able to polymerize at room temperature and harden more quickly. This is a real technological breakthrough compared to epoxy thermoset resins, for example , which need processes that are often more costly and energy intensive as they need to be heated to harden.
What applications are you aiming for?
G.C. – There is a wide range of uses, owing to Elium® resin’s intrinsic qualities. It can be used to make a number of composite materials—with fiberglass, carbon, natural fibers—even with a very high rate of fiber. Arkema is a world market leader in specialty materials and this dominance means that we can target a number of industrial uses with Elium®.
What industries are you targeting with Elium®?
G.C. – The advantages of this resin primarily concern wind power, construction and civil engineering, transportation and hydrogen storage, as well as sailing. Elium® is used in wind turbine blades, composite reinforcement bars for concrete (rebars) in the civil engineering sector, in hydrogen tanks and in sailboat hulls.
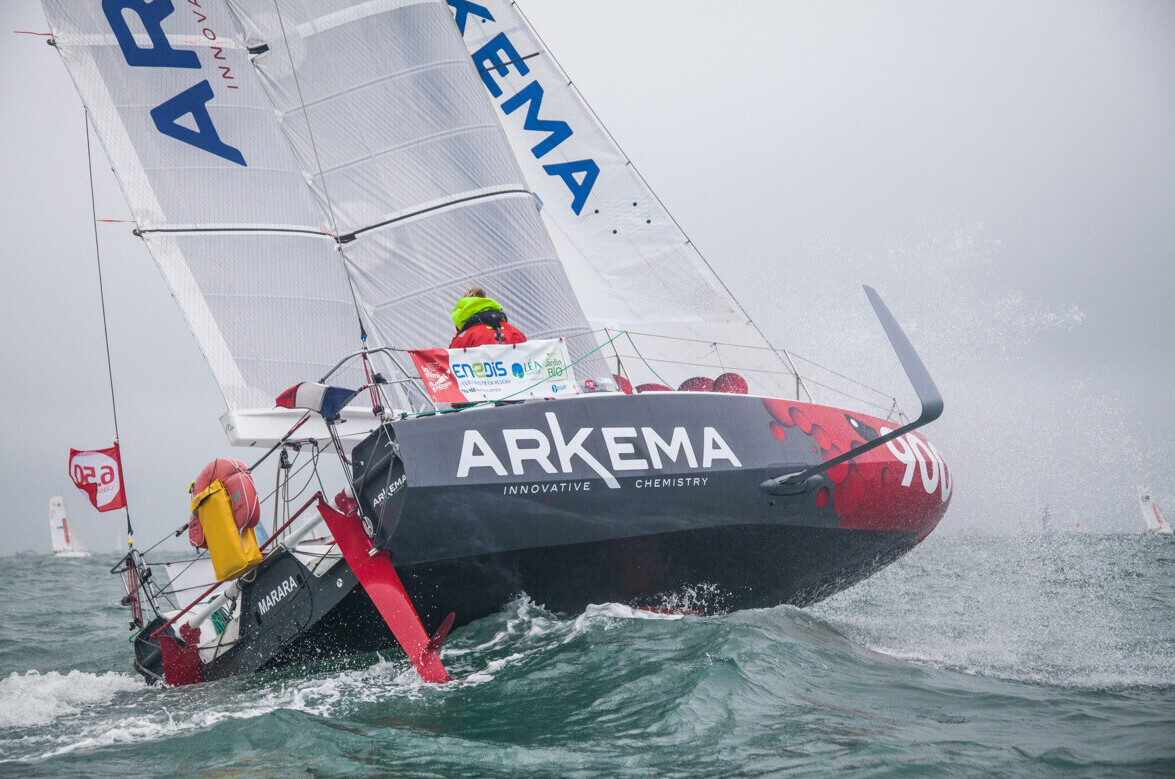
Each industry has its reasons for using Elium®, but our main customers report three main benefits, in addition to the ease of use for a thermoplastic composite material: performance, improved productivity in using the resin and recyclability.
What stage of development are you at?
G.C. – We started production in 2014 in three continents (Europe, North America and Asia). Our customers are now starting to incorporate it into their products. These include LM Wind Power’s wind turbine blades, start-up Northern Light’s sailboats and, very soon, Sireg’s hydrogen tanks and composite reinforcement bars. Elium® sales are increasing sharply in all these markets and Arkema has trebled its annual sales since 2016.
Reasons to be proud of this invention?
G.C. – Our teams are extremely proud in more than one regard. Obviously for the reasons stated above, and because of the feedstocks selected for the formulation of Elium® resin. It contains no cobalt salts, typically used as catalysts to initiate the radical polymerization of the resins, but often classified as carcinogenic in Europe (CMR substances – ), or styrene, which is toxic to reproduction and also classified as hazardous to human health.
How is Arkema establishing itself in this market?
G.C. – We face two challenges: maintaining a high rate of production, driven by brisk demand, while also ensuring uniform quality. So we are developing a global supply chain, setting up our production plants on three continents. But the main thing is to work with our customers and partners on creating a composites production industry that includes the new Elium® resin. We want to give them the broadest overview of the product for their applications. For Arkema, this is one more reason to be proud.
In addition to customers, which partners are involved in the venture?
G.C. – We are working with academics, institutional partners and research centers to create a complete ecosystem centered around Elium® resin. They are helping us to establish it in specific markets. In wind power, for example, with the National Energy Lab in the United States, and in France as part of the ZEBRA (Zero wastE Blade ReseArch) project, coordinated by the Jules Verne research institute to develop zero waste wind turbine blades. All play a necessary role in establishing this new segment. ■
See also
Back to all articles- Expertise articles
- Expertise articles
- Expertise articles