Elium® Thermoplastic resin for recyclable composites
- Africa
- Asia Pacific
- Europe
- Latin America and the Caribbean
- Middle East
- Northern America
- Oceania
Related products
-
Brochure_ELIUM_2024
Latest news
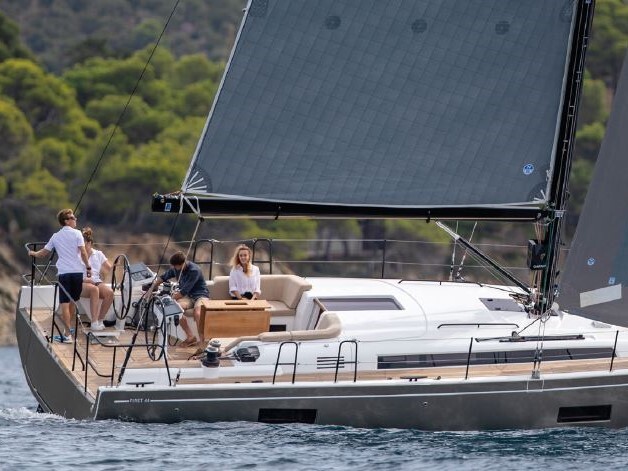

Next events
Booth #C44
Join us to discover our global offer of thermoplastic resins, adhesives and high performance ...
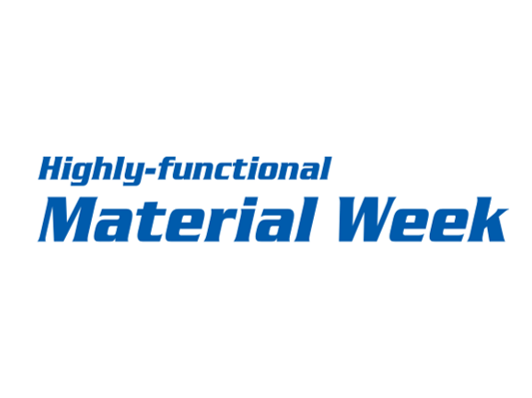
Let's join to discover our protfolio of solutions for ...
Booth #B418
Join us to discover our portfolio of solutions for inside and outside the battery cell
From October 06 to 09, 2025
Booth #5003
Join us to discover our portfolio of solutions for inside and oustide the battery cell
How Elium® thermoplastic resin works
- Formulation: Elium® is a acrylic base polymer diluted in a reactive monomer blend with processing additives that makes it very fluide
- Polymerisation: a polymerisation initiator is mixed with the resin to create an high molecular weight thermoplacstic matrix. Several type of reaction and intitiators are possible
- Process: as a thermoset resin used in composites fiber reinforced polymer. Elium® is compatible with traditional process and the parameters can be adjusted depending on the requirements (viscosity, time and temperature reactivity)
- Applications: our solution enables to obtain high performance composites products like epoxy, polyester or vinylester with all the benefits of thermoplastic matrix. Industries: wind energy, construction and civil engineering, transportation, marine, sports and consumers goods
- End of life: Elium® can be recycled with 2 methodologies, mechanical or chemical, to produce new recycled composites parts.
INNOVATIVE WITH, our magazine with the ideas of the future
Catch up on the full potential of the Elium® resin in the second issue of our INNOVATIVE WITH magazine. Thermoplastic, liquid, easy to process and designed to make composites fully recyclable, Elium® resin ticks all the boxes. A unique resin in the world for thermoplastic composites, whereas traditional thermoset-based composites, widely used in many applications for their light weight and sturdiness, have the disadvantage of not being recyclable at their end-of-life. This innovation is going to revolutionize the wind power, boat-building, hydrogen tank, and concrete reinforcement sectors. But then, for the best testimonies, read our partners’ and customers’ opinions in this latest edition!
Benefits of Elium® thermoplastic resin
A composite part made with our Elium® resins:
- Is light and tough with superior properties under impact
- Is Styrene free, contains no BPA and cobalt salts
- Is fully recyclable with possible separation of the fibers and reuse of the virgin resin
- Has a cost efficient and lower Capex compared to similar thermosets parts
- Has additional features and benefits for adhesion, welding, thermoforming.
Explore our solutions to recycle composites parts using Elium® resin
In 2017 our R&D teams were heavily involved in developing the recycling process for composite parts made from the Elium® resin via depolymerization. The principle entails coarsely crushing the parts; the Elium® resin is then heat-depolymerized so that it can be recovered and purified into a resin with the same properties as the virgin resin. Meanwhile, the remaining carbon or glass fibers can be reused.
Being able to recycle parts made from Elium® resin is a tremendous asset, in particular for wind turbine manufacturers who currently use non-recyclable epoxy resins to manufacture the blades.
Will composites transform industry?
Over the past few decades, composite materials have penetrated all sectors of industry. In a market ultra-dominated by thermosetting composite materials, thermoplastic composites are gradually making their mark.
And future innovations, in particular with regard to recycling, should enable them to gain a lasting foothold.
Arkema acknowledges the support of public funding from EIT Rawmaterials, ADEME (Fr) and the French Investissements d'Avenir Programme in the development of its Elium® range of resins.
This activity has received funding from the European Institute of Innovation and Technology (EIT), a body of the European Union, under the Horizon 2020, the EU Framework Programme for Research and Innovation.