Jul 7, 2025 - 2 min
Mass balance: an innovative approach to integrating more bio-based materials into industry
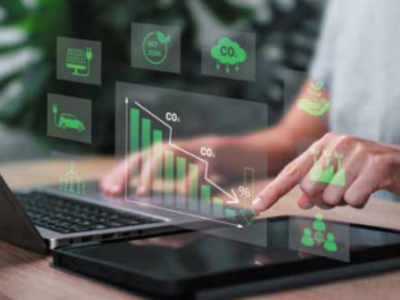
An emerging concept currently being adopted in the chemical industry, the mass balance approach, also known as “bio-based,” is a useful lever for integrating more renewable resources into production right now—without having to change processes—and reducing the carbon footprint of finished products. Here's how it works.
What is mass balance?
On a given production line that produces, for example, 100 batches, introduce a portion of a bio-based version of resource A, equivalent in quantity to the production for one batch. The fossil and bio-based raw materials are then mixed in the same active ingredients. Upon arrival, out of the 100 batches obtained, you can then offer interested customers either a single batch that is fully bio-attributed for raw material A, or two batches that are 50% bio-attributed (or four that are 25% bio-attributed), duly certified as such by the set of valuable certificates, which will not be available to customers of other batches.
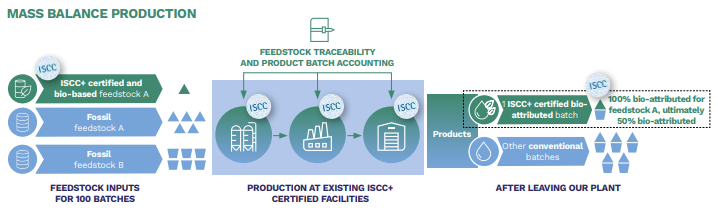
This is the concept of mass balance, or bio-allocation, which has been developing in the chemical industry for several years and for which Arkema has chosen the mass balance method. “This principle, which is similar to what is done for energy with green electricity certificates, has three advantages in materials chemistry,” explains Sylvie Despret, Sustainable Offer Manager at Arkema. First, it allows us to start integrating renewable resources into production, even when they are only available in small quantities. Second, this contribution is made without modifying existing industrial tools. And above all, the performance of the final products remains unchanged, which means that customers do not have to reformulate their products."
Ultimately, “bio-attributed” batches—for which the initial quantity of renewable raw materials is guaranteed by a specific number of certificates—meet the expectations of customers, who can highlight this in their communications. And these customers, who benefit from their certificate attesting to the bio-based content at the outset, make a very real contribution to the decarbonization of the value chain.
Mass balance certification: guaranteeing the traceability of bio-based content from raw material to finished product
Although simple in principle, mass balance requires rigor and transparency in its implementation. The methodological framework is set by ISCC+, an international NGO, and the entire value chain must be certified and audited annually to ensure traceability from the raw materials of origin to the finished product. “ISCC+ certification, which is obtained at the plant level for one year, certifies, among other things, the implementation of a flawless traceability system for raw materials and the accounting of produced batches,” says Sylvie Despret. This is a real commitment of resources for manufacturers. " In practice, the decision to develop a mass balance offering is therefore made on a case-by-case basis, depending on the availability of bio-based or recycled raw materials and the maturity of the markets and consumer confidence.
Which products are covered by the mass balance approach?
At Arkema, this lever is now an attractive way to accelerate the replacement of fossil-based raw materials with bio-based raw materials in certain production processes. This is the case for certain Bostik products, as well as for Kynar® PVDF, for which bio-based grades have been available since 2024. However, it is mainly within the Coating Solutions segment that the mass balance offering has developed, driven by market demand. The ultimate goal is to support the development of more sustainable solutions for coating/protection applications in batteries, advanced electronics and construction (paints, varnishes, etc.)
“We have ISCC+ certified the majority of our sites in Europe and Asia and have obtained our first certifications in the US, enabling us to offer a bio-attributed range with a lower carbon footprint to interested customers for almost all of our products through the use of raw materials based on recycled cooking oils,” explains Hélène Pernot, Marketing Director for Sustainable Products. Initial sales have started with paint manufacturers in the decorative paint, industrial wood, and powder coatings markets for the construction industry. Finally, it should be noted that Arkema has adopted the most stringent definition of mass balance for all these products: “We use the ‘mass balance’ approach, according to which bio-based raw materials must actually enter the manufacturing chain of the finished product—and the final product must consist of mixed raw materials,” explains Sylvie Despret. Did you say “transparency”?
What is the difference between mass balance and bio-based?
In parallel with its mass balance approach, Coating Solutions has long been developing a range of bio-based solutions using the traditional “segregated” approach (where the bio-based content is inherent in the production process) – such as the Synaqua® range of resins with a high vegetable biomass content.
In 2024, the segment extended this bio-based offering to other products, thanks to a major change in sourcing at its Carling site in France, where ethyl acrylate, which contains 40% ethanol, is now produced from bioethanol derived entirely from plant-based materials. “We therefore have a 40% bio-based ethyl acrylate,” summarizes Hélène Pernot, Marketing Director for Sustainable Coating Solutions. "This is a key product that feeds into our entire downstream supply chain. " This is the case, for example, with a range of high value-added resins for the textile industry and a range of specialty thickening agents widely used in the paint industry—now bio-based up to 30% and enabling a carbon footprint reduction of up to 40%.
See also
Back to all articles- Case Study
- Case Study
- Expertise articles