Jul 25, 2025 - 3 min
The shift of hydrogen clean energy
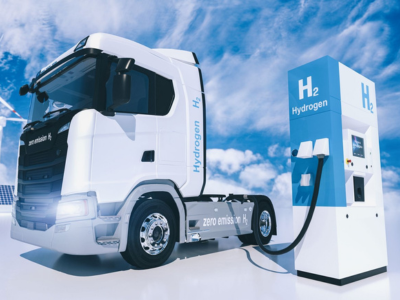
In recent years, many countries have embraced hydrogen as a way to align their industrial ambitions with the urgent need for an energy transition. Indeed, many industries still rely on processes that are both energy-intensive and high in carbon emissions. Hydrogen offers a promising alternative, replacing certain fossil fuels or carbon-based reactants, thus helping to reduce the carbon footprint of a number of industrial activities.
Hydrogen also shows strong potential in the mobility sector. This is because it mainly emits water during use and, in the case of direct combustion, only a small amount of NOx (nitrogen oxides), similar to those already treated on conventional vehicles. In any case, it no longer emits carbon. In addition, its high energy density gives hydrogen-powered vehicles a greater range than other alternative propulsion systems, such as fully electric cars.
Today, the hydrogen market is undergoing major changes, aiming to identify not only the most low-carbon production methods, but also the most scalable applications. The goal is to optimize this solution to make it even more relevant for large-scale use.
How is hydrogen produced?
To make sure that hydrogen answers energy transition challenges, the way it is produced must evolve. As of now, most of the hydrogen produced worldwide comes from methane reforming, a cost-effective process but one that emits significant amounts of carbon. This is known as grey hydrogen. In contrast, low-carbon hydrogen, produced via water electrolysis powered by renewable sources like wind or solar, still plays a marginal role.
To give hydrogen mobility real meaning, the question of production is the starting point. Being able to produce low-carbon hydrogen is essential to enabling the energy transition across multiple sectors."
The challenge of developing green hydrogen
To generate a truly positive energy impact, grey hydrogen must gradually be replaced by its lower-carbon counterpart.
The figures speak to the necessity of this transition. Low-carbon hydrogen is making progress: final investment decisions (FID) had already doubled by 2023, bringing total planned production capacity to 3.4 million tons per year[1]. Still, that is not enough to meet the growing demand, with more than 97 million tons used globally in the same year[2]. Moreover, hydrogen from low-emission sources accounts for less than 1% of this total consumption[3].
At the global level, hydrogen production dynamics vary significantly. Asia stands as the world leader in this field. China in particular benefits from a well-established industry and extensive logistical capacity. It is therefore the largest hydrogen producer, with over 30 million tons produced annually[4], still mostly from carbon-based processes. Europe and the United States are also active, investing in the production of low-carbon hydrogen. In Europe, for instance, installed electrolyzer capacity reached 385 MW as of September 2024[5].
To put it briefly, low-carbon hydrogen production capacities are growing globally, as the sector increasingly recognizes that this issue is a central challenge for its own development. In the meantime, the market itself is becoming more and more segmented, with a growing focus on identifying the most promising applications.
Hydrogen for decarbonized heavy-duty mobility
The hydrogen mobility market is now moving toward greater rationalization. Efforts are indeed progressively focused on applications for heavy-duty mobility. As mentioned earlier, hydrogen holds a high amount of energy per unit of mass. At the same time, however, its volumetric energy density is much lower, meaning it needs to be compressed or liquefied to be stored in reasonable volumes. These characteristics make hydrogen particularly well suited for intensive use and long-distance transport, where space constraints are less critical. It is therefore a highly complementary solution to electric mobility.
Hydrogen mobility is still generally in an experimental phase. For example, hydrogen heavy-duty trucks accounted for only 0.3% of global sales in 2024. “Our goal is to support this momentum and offer solutions to the challenges facing the market.”
Although projections for hydrogen mobility remain uncertain, it continues to be a core topic in the energy transition. In other words, hydrogen is a promising pathway, but one that requires large R&D and infrastructure investments to reach maturity and scale-up. Its deployment will inevitably take time.
The challenge of hydrogen safety and storage
Beyond production, hydrogen also presents challenges directly related to its physical properties. It is a gas that is both highly volatile and flammable. Safety and storage are therefore critical issues: the materials used to transport hydrogen must be robust enough to withstand even extreme conditions. In addition, their structural integrity must be regularly monitored to detect potential weaknesses and prevent leaks.
Economic viability is a key concern as well. Electrolyzers used to produce low-carbon hydrogen are expensive and still not widely deployed on a global scale. The cost of building a hydrogen-powered vehicle is also high, due to the advanced technologies it requires, such as the storage tank and fuel cell. It is therefore up to players like Arkema to develop solutions that can deliver performance gains and, over time, lead to cost savings.
Finally, recyclability is emerging as a key issue. Hydrogen management systems, such as storage tanks, are currently expensive because they rely on high-performance materials, particularly carbon fiber. Incorporating recyclable materials would make it possible to recover value at end of life, reduce the overall system cost, and improve its long-term economic viability. This example shows that, in some cases, recyclability and costs are closely linked.
Arkema's offering for hydrogen production and use
Across the entire hydrogen value chain, all the way to the vehicles themselves, Arkema actively addresses these challenges. The Group designs solutions that make each step more efficient, more reliable, safer, and more cost-effective.
Starting at the production stage, Arkema’s high-performance polymers can be used in the pipes and connectors of electrolysis units. Their excellent thermal, mechanical, and chemical resistance makes them valuable assets for extending the lifespan of these systems.
“Further upstream in the production chain, molecular sieves are another key component of this value chain,” explains Thomas Fine. “They are used to dry and purify the hydrogen produced through electrolysis”.
To enhance the performance of this step, Arkema has developed the Siliporite®H2SIEV molecular sieves range. Its high capacity enables fast hydrogen drying, while its high density allows for more compact units, reducing space requirements — ultimately making this step more efficient and cost-effective. Finally, the Group’s materials also contribute to making hydrogen transport safer. At the plant exit, for example, the Spotleak® blend is used to odorize hydrogen, making it easier to detect in the event of a leak.
Within hydrogen-powered vehicles themselves, there are also numerous examples of Arkema material applications. For example, to address permeability challenges, the Group has developed hydrogen tightness layers made of Rilsan® Polyamide 11. This polymer is highly resistant to external stress and leakage, and is used in distribution lines as well as in the liner, which is the inner wall of hydrogen tanks. It ensures both efficient and reliable distribution.
Finally, the Elium® thermoplastic resin can be used for the carbon fibers composites envelope of hydrogen high-pressure vessels, able to withstand 700 bar pressure. This material offers a sustainable alternative to traditional epoxy resins, with a major advantage in terms of recyclability. Unlike thermoset resins like epoxy, this thermoplastic alternative, is enabling the recovery of the carbon fibers and the resin by depolymerization at mild temperature.
But Arkema’s solutions for hydrogen mobility go even further! From smart tapes with piezoelectric sensors to monitor tank performance to ultra-resistant, lightweight UDX® tapes for composite pressure vessels — learn more about our innovations in this video from the latest JEC Group Composites show.
Preparing for the future of energy
In the future, Arkema will continue to support the market’s transformation and seek innovative solutions to its ongoing challenges. In this regard, strengthening the low-carbon hydrogen sector — in which the Group has strong confidence — remains a key focus area.
“Looking ahead, what seems most realistic to us is a more pronounced market segmentation in favor of energy intensive mobility like trucks or light duty vehicles,” concludes Jean-Paul Moulin. “It’s up to Arkema to address these short-term challenges while continuing to identify the areas where we can best support the energy transition.”
Beyond road mobility, aviation and maritime transport are also sectors where hydrogen and its derivatives could hold strong potential. Both are energy intensive mobility markets, with high fuel consumption and significant carbon emissions. However, these applications raise critical questions around production capacity and hydrogen availability. Meeting this large-scale demand will require major infrastructure development, a key challenge for the years ahead.
See also
Back to all articles- Expertise articles
- Case Study
- Webinar