8 mars 2019 - 7min
Les solutions d’Arkema pour des voitures électriques plus performantes
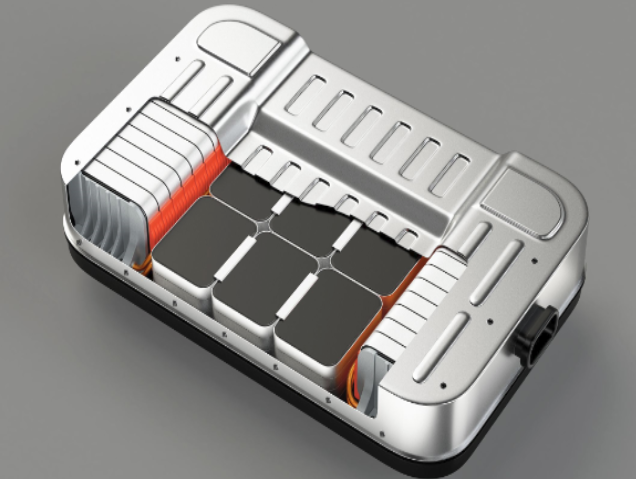
La technologie des batteries lithium-ion s’est considérablement améliorée ces dernières années. Arkema y a contribué avec son PVDF Kynar® et continue de collaborer avec les fabricants de batteries pour optimiser encore l’autonomie, le temps de charge et la durabilité de ces batteries. Ses chercheurs s’intéressent aussi aux technologies du futur. Le point avec trois experts Arkema: Thomas Fine, Responsable développement batteries pour les polymères techniques, Philippe Bonnet, Directeur R&D produits fluorés, et Dominique Plée, Directeur scientifique en charge des batteries.
Pouvez-vous rappeler le principe de fonctionnement d’une batterie lithium-ion ?
Thomas Fine - La batterie lithium-ion s’appuie sur une réaction chimique réversible pour faire circuler des ions et électrons et générer ainsi de l'énergie électrique. Chaque batterie rassemble des centaines voire des milliers de cellules, chacune constituée de trois éléments : une électrode négative ou anode (une feuille de cuivre, collecteur de courant sur laquelle sont collées des particules de graphite qui vont "capter" les ions lithium au moment de la recharge), une électrode positive ou cathode (une feuille d’aluminium, collecteur de courant sur laquelle sont collées des particules métalliques qui vont "capter" les ions et électrons au moment de l’utilisation de la batterie). Et enfin, au milieu, un film séparateur poreux (pour laisser passer les ions) qui joue le rôle d'isolant électrique afin que les deux électrodes ne se touchent pas.
On injecte ensuite dans la cellule l’électrolyte, un solvant liquide dans lequel sont mis des sels de lithium. Ces sels sont à l’origine des ions qui vont passer de l’anode à la cathode en traversant le séparateur, lorsque la batterie est en activité ; les électrons simultanément passent de l’anode à la cathode par le circuit externe, c’est-à-dire par les différents composants de la voiture qui sont alors alimentés en électricité. En charge, les ions et électrons font le chemin inverse, de la cathode à l’anode.
Ces cellules sont ensuite empilées dans des contenants "packs" rassemblés dans un caisson, le "casing" placé sous la voiture. À titre d’exemple, le caisson des voitures électriques comme Tesla peut contenir plusieurs dizaines de packs, c’est-à-dire jusqu’à 7000 cellules.
Fabrication des électrodes : le savoir-faire d’Arkema pour améliorer leur productivité
Les constructeurs de batteries et de véhicules électriques s’intéressent à la fabrication d’électrodes par extrusion, procédé innovant et très performant. Ce procédé permet de gagner en productivité, d’économiser des solvants et de diminuer les investissements et les coûts de fabrication. Acteur incontournable dans la transformation des polymères, Arkema maîtrise parfaitement l’extrusion, étape clé dans ce procédé.
Comment Arkema a-t-il contribué aux améliorations de performances des batteries lithium-ion ces dernières années ?
Thomas Fine - Notre PVDF Kynar®, un polymère fluoré très résistant aux voltages élevés et au solvant de l’électrolyte, est largement utilisé dans les batteries lithium-ion pour deux fonctions essentielles : il sert de "liant" pour coller les particules actives entre elles et sur le collecteur de courant mais aussi de revêtement de protection du film séparateur. Sans ce liant suffisamment résistant dans les électrodes et sans une protection efficace du séparateur, les ions et les électrons circulent de manière chaotique entre la cathode et l’anode. Le séparateur est alors très sollicité en phase de charge comme de décharge, les ions et les électrons suivant des trajectoires désordonnées. Avec à la clé des déperditions d’énergie et une usure du séparateur et donc de la batterie.
Dans une batterie lithium-ion qui utilise du PVDF Kynar®, les ions et les électrons circulent plus efficacement, en recharge comme en décharge, contribuant à la performance des batteries. Sur le séparateur, la grande résistance électrochimique de notre PVDF participe à la longévité des batteries. Depuis 15 ans, nous avons continuellement amélioré nos grades : cela a permis aux fabricants de batteries d’en réduire les quantités nécessaires sur les électrodes - la quantité passant progressivement de 8 % de la formulation à 1,5 % aujourd’hui - et d’augmenter d’autant les quantités de particules actives qui attirent les ions et électrons, amplifiant ainsi la densité énergétique de la batterie.
Le PVDF Kynar® est utilisé par de nombreux fabricants de batteries lithium-ion, notamment en Chine où Arkema a répondu présent au moment du boom de la voiture électrique avec son usine de Changshu qui a été en capacité de produire les bons grades. Nous sommes notamment le partenaire de CATL - le plus gros fabricant chinois de batterie au monde - depuis sa création en 2011 et grâce à cette collaboration, nous avons pu améliorer continuellement nos grades pour les batteries.
Quelles autres pistes explorez-vous pour optimiser encore les performances de la batterie lithium-ion ?
Thomas Fine - Aujourd’hui l’enjeu R&D des fabricants de batteries est de faire baisser le coût de fabrication des batteries mais surtout d’augmenter l’autonomie (c’est-à-dire dépasser les 400 km sur autoroute), d’accélérer la vitesse de recharge (on vise des charges de 80 % de la batterie en 15 mn) et d’allonger la durée de vie des batteries (c’est-à-dire dépasser 1 000 cycles de recharges/décharges complets). S’il est encore possible d’améliorer les temps de chargement sur la technologie des batteries lithium-ion actuelle, cela peut provoquer des altérations qui limitent la durée de vie de la batterie, voire suscitent une instabilité qui peut amener à l’inflammation. Les fabricants doivent donc trouver le bon compromis afin d’améliorer les performances de la batterie, tout en s’appuyant sur des matériaux parfaitement stables. Notre Kynar® très résistant aux hauts voltages joue un rôle très important dans cet équilibre.
Philippe Bonnet - Notre R&D s’investit aussi sur d’autres matériaux dont les fabricants de batteries attendent beaucoup. Nous travaillons notamment, grâce à notre expertise dans la chimie du fluor, sur de nouveaux sels d’électrolytes (les LI-FSI et les LI-TDI) beaucoup plus stables aux hauts voltages que les sels d’électrolytes actuels. Ils permettront d’améliorer, sans aucun risque d’implosion, l’autonomie de la batterie, son temps de charge mais aussi sa durée de vie.
Dominique Plée – Un autre levier d’optimisation est l’ajout dans les cathodes, en complément d’autres charges carbonées, de nanotubes de carbone (NTC), des additifs reconnus pour leurs propriétés de conductivité électrique. Rajouter environ 2% de NTC dans la formulation de la cathode favorise le passage des électrons, donc de l’énergie, de la cathode à l’anode, permettant ainsi une charge plus rapide des batteries. Arkema, l’un des rares producteurs au monde de NTC, travaille actuellement à la mise au point d’un procédé pour purifier ces nanotubes afin qu’ils soient exempts de toute trace de catalyseur métallique et qu'ils soient parfaitement stables dans une batterie.
Il est question d’autres technologies de batteries : lithium-soufre, tout solide… êtes-vous sur ces technologies ?
Dominique Plée - Oui, nous nous devons bien sûr d’anticiper les technologies de plus long terme. Nous sommes donc impliqués en R&D sur la batterie lithium-soufre en collaboration avec la société Oxis les applications de ces batteries ne sont pas aujourd’hui les voitures, mais tout ce qui vole (satellite, drone, avionique), c’est-à-dire ce qui nécessite des gains de poids au kWh embarqué, car elles sont plus légères que les batteries lithium ion. Oxis espère améliorer, grâce à sa collaboration avec Arkema et d’autres partenaires, ses batteries de façon à pénétrer le marché du gros transport.
Nous regardons aussi bien sûr aussi la technologie de la batterie dite "tout solide", que certains considèrent comme une technologie de rupture et la véritable batterie du futur. Il s’agit de remplacer l’électrolyte liquide – la substance conductrice de l’électricité – par une plaque conductrice de céramique ou de polymère qui jouerait aussi le rôle de séparateur. Cette technique permettrait de réduire les risques d’inflammation de la batterie lithium-ion liquide mais surtout assurerait des performances hors du commun : autonomie de 600 km, voire 800 km et temps de recharge réduit à quelques minutes. Dans notre laboratoire commun avec Hydroquebec nous nous intéressons déjà à cette technologie dans laquelle des polymères spécifiques pourraient jouer un rôle important en tant que séparateurs conducteurs et composants de catholyte (un mélange de matière active et d’électrolyte). Toyota parle d’un premier modèle fondé sur cette technologie à l’horizon 2025. D’autres constructeurs annoncent 2030. Les avis divergent sur la date d’industrialisation de cette technologie, mais cela sera sans conteste une rupture dans le monde des batteries. En attendant, les batteries lithium-ion qui s’appuient sur une technologie mature, ont encore de beaux jours devant elles d’autant que les matériaux qui peuvent améliorer leur efficacité sont clairement identifiés. Ce qui est sûr c’est qu’une seule technologie ne répondra pas à tous les besoins.