7 mars 2019 - 8 mn
Résine Elium®: une innovation de rupture dans le monde des composites ?
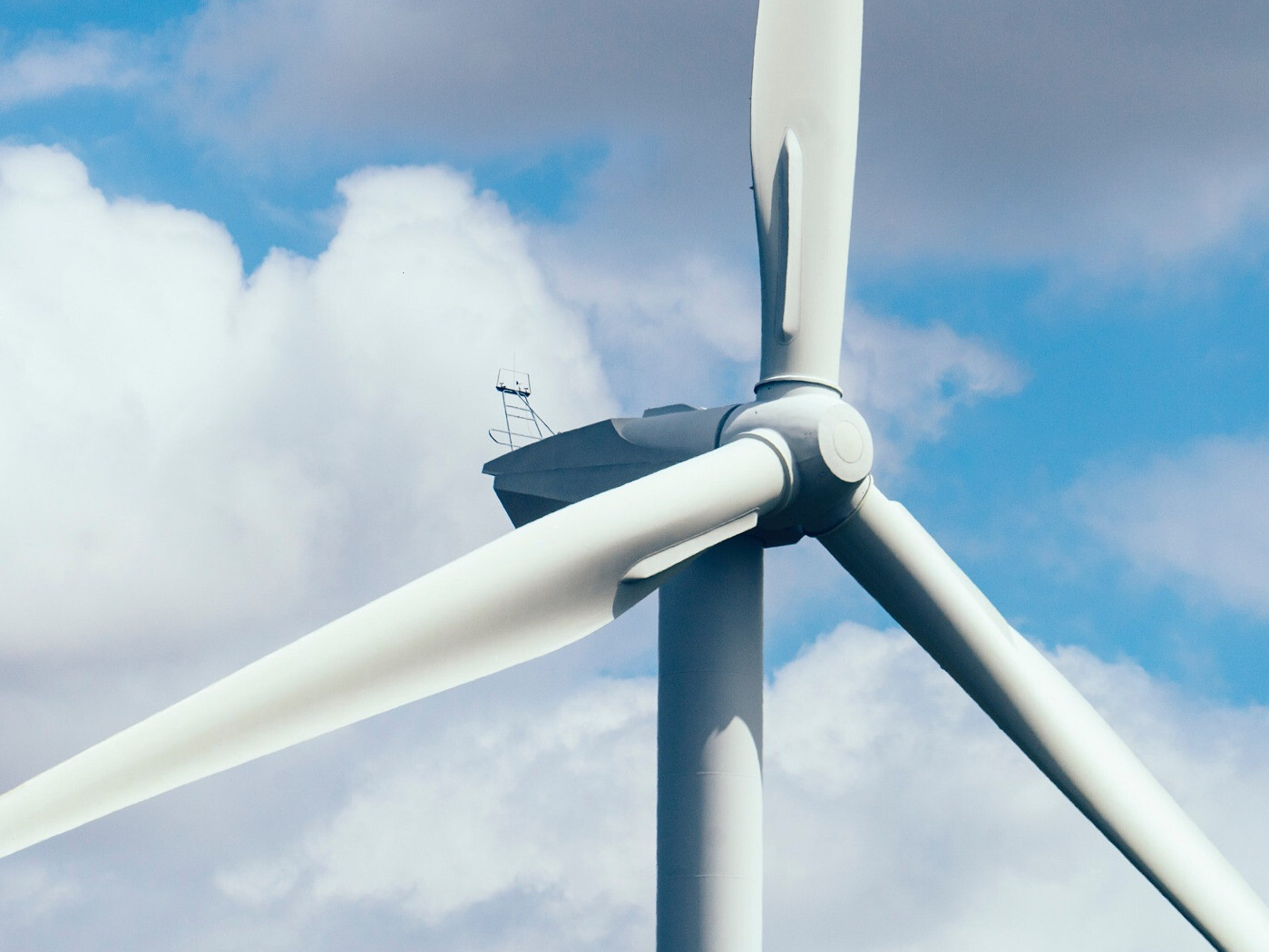
Avec sa résine liquide thermoplastique Elium®, Arkema offre une solution unique sur le marché pour fabriquer des pièces composites selon les mêmes procédés de fabrication que ceux utilisés pour les pièces en résines thermodures déjà en place chez les transformateurs. Avec l’atout majeur de la recyclabilité, mais aussi du thermoformage et du thermosoudage. De nombreux secteurs pourraient bénéficier de ces points forts : l’éolien, l’automobile mais aussi la construction et le sport.
La prochaine génération des pales d’éolienne sera en composites thermoplastiques
Cette déclaration en ouverture de la conférence internationale Wind Turbine Blade Manufacture à Düsseldorf en décembre 2018, de Bart Roorda, CTO de Sinoma, l’un de principaux fabricants de pales d’éoliennes en Chine, donne la tendance. Aujourd’hui les pales des 20 000 éoliennes – soit environ 550 000 tonnes de composites ! – installées partout dans le monde chaque année sont en composites thermodurs base résines époxy/fibres de carbone ou de verre. Leurs propriétés de légèreté, de solidité et de résistance aux chocs en font des matériaux de choix pour cette application. Mais ils présentent un inconvénient de taille : ils ne peuvent pas être refondus et la question de la fin de vie de ces composites utilisés pour ces pales - mais aussi pour de très nombreuses autres applications - risque de poser un sérieux problème environnemental d’ici quelques années.
Vents porteurs pour Elium®dans l’éolien
Le parc mondial des éoliennes connaît une croissance chaque année entre 10 % et 15 % (source : Global Wind Energy Council). Sur ce marché en plein essor, la résine thermoplastique Elium® permettant de fabriquer des pales en composites recyclables représente donc une véritable innovation et une alternative prometteuse. Convaincu du formidable potentiel de cette résine, Arkema s’est lancé dans plusieurs projets collaboratifs visant à démontrer la faisabilité de la fabrication industrielle de pales prototypes en résine Elium® selon les procédés couramment utilisés pour les pales en résines époxy.
En France, Arkema a fait équipe avec Plastinov et d’autres PME innovantes au sein du projet Effiwind, soutenu financièrement par la région Aquitaine et l’Ademe, avec comme enjeu de réaliser des pales en résine Elium® fibres de verre permettant de produire de meilleurs rendements en énergie. Le procédé de fabrication de pales de 25 mètres a déjà pu être validé : « Nous avons confirmé la viabilité industrielle de ces pales et la rapidité de fabrication. Nous sommes maintenant dans une phase de caractérisation des performances du matériau et de tests de dynamique et de résistance de la pale auprès d’un institut indépendant qui permettront d’obtenir la certification DNV.German Loyd fin 2019, le sésame pour pouvoir vendre notre résine aux fabricants de pales » explique Guillaume Clédat, Responsable de développement Elium® chez Arkema.
D’ores et déjà, des premiers tests probants menés en interne par la R&D d’Arkema ont démontré qu’une pièce composite en Elium® est plus résistante dans le temps que des pièces en composite thermodur, avec une tenue à la fatigue 10 fois supérieure.
Aux États-Unis en 2017, c’est au sein de l’Institute for Advanced Composites Manufacturing Innovation (IACMI), le grand programme américain d’investissement dans les composites, qu’Arkema et ses partenaires – dont TPI, le premier fabricant américain de pales – se sont mobilisés pour réaliser un prototype de pale de 9 mètres de long, en composites 100% base Elium® afin de démontrer la simplicité de mise en œuvre par infusion, ses qualités mécaniques et ses bénéfices environnementaux. Liquide tout comme les résines époxy, la résine Elium® a permis d’avoir recours aux mêmes moules que ceux utilisés pour les composites thermodurs.
Mais avec une consommation d’énergie moindre puisqu’il n’a pas été nécessaire de chauffer les moules et que la mise œuvre s’est faite à température ambiante. Autre avantage, les éléments de la pale ont été assemblés très simplement par collage sans apport de chaleur, a contrario des collages thermodurs. Pour certaines parties de la pale, l’assemblage par simple thermosoudage a même été possible, permettant des gains de temps et de coûts de fabrications conséquents. « Nous avons réalisé depuis une nouvelle pale prototype de 13 mètres qui a permis de démontrer un gain de temps dans la fabrication de 20 % par rapport aux pales en époxy » explique Guillaume Clédat.
Arkema relève le défi de la recyclabilité des pièces composites en Elium®
Lorsque les millions de tonnes de pales d’éolienne en composites époxy, mais aussi de composites thermodurs utilisés dans les voitures, avions, camions ou dans la construction vont devoir être recyclées, un enjeu écologique de taille va se présenter. Ces matériaux thermodurcissables sont très difficiles à recycler et le cas échéant, ce recyclage n’est pas économiquement viable. Actuellement ils sont le plus souvent enfouis ou incinérés en fin de vie.
Misant sur la thermoplasticité d'Elium® – c’est-à-dire sa capacité de refonte –, Arkema a déjà pu démontrer la recyclabilité à l’échelle laboratoire de petites pièces en Elium®. Une nouvelle étape est en cours qui vise à démontrer la recyclabilité, à un coût compétitif, de pièces composites en Elium® de très grandes dimensions.
Nous avons fait le choix de recycler une pale de 25 mètres de 2,5 tonnes : cela se fera en trois étapes, coupe en tronçons, puis broyage en granulés et enfin l’étape de chauffe pour dépolymériser ces granulés afin de récupérer la résine Elium<sup>®</sup> d’un côté et les fibres de verre de l’autre. Nous étudions la mise au point d’un procédé suffisamment performant pour produire une résine recyclée compétitive aux qualités identiques à celles d’une résine vierge. Des débouchés seraient alors envisagés pour produire de nouvelles éoliennes ou des pièces pour l’automobile
Une résine polyvalente qui s’adapte à tous les procédés composites
Au-delà du marché potentiellement très important de l’éolien, la résine Elium® permet de fabriquer une grande variété de pièces composites thermoplastiques à fibres de verre ou fibres de carbone continues, de toutes tailles, et de formes complexes. Son atout économique repose sur deux caractéristiques majeures : sa facilité de mise en œuvre avec des temps de durcissement courts à température ambiante et sa compatibilité avec les nombreuses technologies de transformation des résines thermodurcissables, limitant ainsi les investissements pour les transformateurs déjà équipés de ces machines. La formulation Elium® est alors adaptée en fonction des procédés envisagés et des applications visées. Ces technologies sont : l’infusion (technologie utilisée pour les pales d’éoliennes ou encore pour les coques de bateaux – voir encadré ci-dessous), le Resin Transfer Molding (RTM), le Sheet Molding Compound (SMC), la pultrusion et les tapes imprégnés.
Arkema s’attache à tester sa résine sur tous ces procédés en s’associant avec de grands transformateurs afin de fabriquer des pièces spécifiques pour les marchés visés.
Les procédés de moulage RTM et SMC pour des pièces automobiles ou ferroviaires
En partenariat avec l’Institut de recherche technologique de Metz (IRT-M2P) et plusieurs constructeurs et équipementiers automobiles français, Arkema s’est engagé dans le projet Fast RTM en 2016. « Nous avons créé un pilote industriel afin de démontrer la possibilité de produire en grande série des pièces automobiles – de carrosseries ou structurelles – en composites Elium® et matrices fibres de verre ou carbone, aux cadences exigées par les constructeurs : une pièce toutes les deux minutes », explique Michel Glotin, Directeur scientifique matériaux chez Arkema.
Ce projet a permis de valider qu’une intégration rapide de pièces composites en résine Elium® pourrait s’opérer sur les chaines de production automobile. Dans le cadre d’un projet Européen soutenu par l’European Institute of Technology - Raw Materials (Berlin), en collaboration notamment avec le partenaire espagnol Mondragon-Batz, des pièces structurelles de renfort de porte anti-intrusion ont pu être fabriquées en composite à base de résine Elium® selon ce procédé.
Autre technique éprouvée, la SMC (Sheet Molding Coumpound) un procédé bien connu et répandu chez les transformateurs de résines thermodures. Par ce procédé, en partenariat avec le chimiste allemand BYK Chemie et le formulateur fabricant mondial de composites thermodurs IDI, Arkema est parvenu à produire des pièces en Elium® chargées en fibres de carbone à un coût très compétitif. Ce procédé est utilisé pour le moulage en compression – souvent de très grandes pièces ou de pièces complexes – où de hautes résistances mécaniques sont exigées. Un excellent aspect de surface, ignifuge et une isolation électrique importante font du composite en Elium® fabriqué par SMC le matériau idéal pour les panneaux de carrosserie et diverses pièces structurelles automobile ou ferroviaires. Des pièces composites conçues par SMC sont envisagées notamment pour remplacer le métal dans les caisses en blanc et autres pièces de structure des voitures. 30 à 50 % plus légères que les mêmes pièces en acier, et tout aussi résistantes, ces pièces en Elium® répondent à l’enjeu sociétal de l’allègement de l’automobile.
Le procédé de pultrusion pour des barres de renfort de bétons et câbles pour bétons précontraints
La résine Elium® a également été testée sur des machines de pultrusion standard, toujours avec l’IRT M2P de Metz, afin de produire des câbles et tiges ultra-résistants. La maîtrise de cette technique de fabrication ouvre des perspectives principalement dans la construction avec une application phare : les barres de renfort de béton armé chargées en fibres de verre. Celles-ci viendront remplacer des armatures en métal couramment utilisées dans le BTP avec l’avantage de la résistance à la corrosion dans les ouvrages exposés à des environnements difficiles comme le milieu marin. Ces tiges de renfort en composite base Elium® présentent surtout un atout considérable sur les barres de renfort rigides en composite thermodur déjà utilisées dans certaines constructions : « elles peuvent être « cintrées » par thermoformage, elles sont donc parfaitement adaptées pour la consolidation des structures complexes. Cela réduit les coûts de mises en formes pré-personnalisées », explique Guillame Clédat, à l’origine de ce développement.
Une autre application visée par Elium® grâce à la maîtrise du procédé de pultrusion : les câbles d’armatures pour bétons précontraints utilisés dans les constructions de ponts à voussoirs, afin de remplacer les torons et câbles d’acier souvent sujets à la corrosion. La résine Elium® est renforcée par de la fibre de verre par pultrusion puis plusieurs joncs pultrudés sont combinés et thermoformés pour constituer le câble.
En vue d’expérimenter ces deux développements prometteurs dans le BTP et le génie civil, Arkema s’est associé avec la société italienne Sireg, fabricante de composites pour la consolidation des sols, de tunnels et autres infrastructures. Des premiers chantiers tests sont déjà envisagés dans plusieurs parties du monde.
Le procédé de rubans imprégnés d’Elium® durcis par UV Initiation
La résine Elium® peut également être utilisée pour imprégner des bandes de fibres de carbone ou des fibres de verre qui sont ensuite déposées sur des préformes par positionnement robotisé : le ruban se déroule et s’imprègne en même temps de résine Elium® avant de se placer sur la forme. Le ruban imprégné de résine est alors instantanément polymérisé par rayon UV. « Ce procédé est très innovant et on gagne du temps car la polymérisation est immédiate » précise Guillaume Clédat.
Grâce à cette technologie, Arkema a déjà conçu avec Mäder (fabricant d’additifs, notamment d’additifs photo-inititeurs) et MF Tech (fabricant machines d'enroulement filamentaire) un réservoir d’hydrogène de 80 litres capable de résister à des pressions très élevées.
Un champ infini d’applications
Les performances mécaniques des composites en Elium® et la polyvalence de cette résine en termes de procédés de transformation ouvre un vaste champ de développements sur une multitude de marchés. « Des pièces dans le secteur du sport ont aussi déjà été produites en composites Elium®: semelles de chaussures de vélo faites en partenariat avec le Singapore Institute of sport Research, raquettes de tennis, cannes de hockey, casques, etc. Depuis la mise sur le marché de la résine Elium®, nous sommes approchés par de nombreuses PME séduites par ses caractéristiques uniques. Cette résine a un potentiel immense dans le contexte de la course aux matériaux toujours plus performants et légers, faciles à mettre en œuvre et surtout recyclables. Nous n’en sommes qu’aux prémices de son développement » conclut enthousiaste Guillaume Clédat.
Elium® « infuse » dans le milieu du nautisme…
Dans le cadre de son sponsoring dans la voile avec le Team Lalou, dès 2016 Arkema a contribué à la construction d’un prototype Mini 6.50, un voilier monocoque dont la coque et le pont ont été entièrement réalisés en résine thermoplastique Elium®, par infusion de fibres de carbone. Après 2 ans de navigation, dont deux transats, le Mini 6.50 a fait les preuves de sa solidité.
Séduite par les performances de ce prototype en Elium®, en 2019, c’est la société bretonne Ouest Composites qui vient de fabriquer la carène d’un bateau semi-rigide en Elium® par moulage infusion, également en collaboration avec Arkema.
Voir aussi
Tous les articles- Article expertise
- Article expertise
- Article expertise