Mar 15, 2023 - 6 mins
Gas leak detection : what is the science behind gas odorization ?
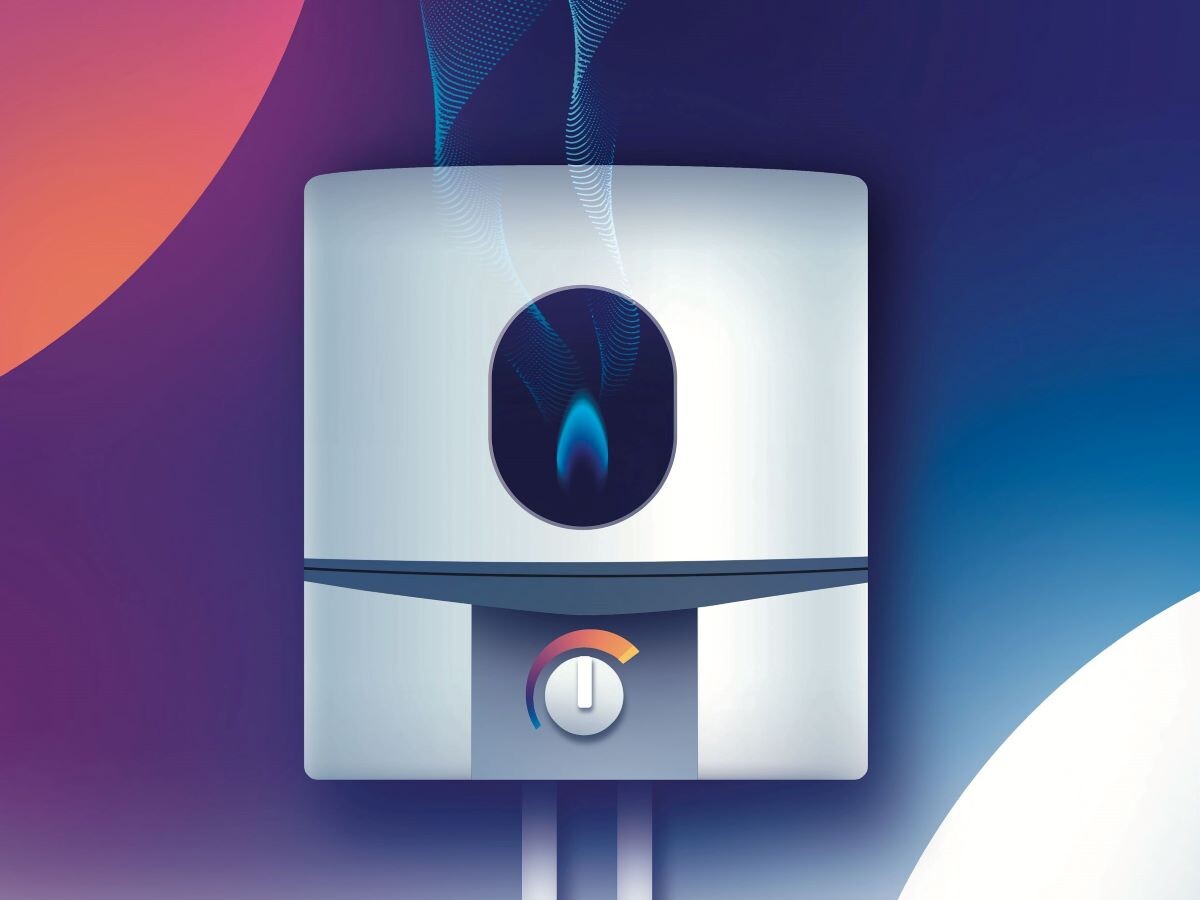
Until the 1950s, coal gas or town gas manufactured for consumers and municipalities was the main source of fuel and lighting in the US and Europe. The manufacturing process of coal gas was highly toxic and gas contained a significant amount of CO (carbon monoxyde). The gaseous fuel was distributed through a distribution system to consumers and could be detected due to presence of impurities that give a distinctive sulfurous smell to the fuel. After World War II, natural gas emerged as less toxic and cleaner energy which led to the gradual development of natural gas supply and transmission infrastructure.
Gas leak accident and regulations
In the aftermath of the tragedy, the first odorization regulation emerged in Texas and then at federal level and is now a widespread documented rule and practice stating that distributed fuel gases should be odorized so that a leak shall be detected before reaching 20% of the LEL.
What are the odorization technologies?
French law requires that gas network operators deliver odorized gas to all consumers However, the in current practice all transported gas is odorized and it is recognized by French authorities as the best practice in safety studies. Meanwhile in Belgium and Denmark regulations do not require odorization of transported gas, whereas, in Spain, it is mandatory to odorize gas during transportation.
Arkema gas odorants: a portfolio of tailored products for different needs
Each type of gas requires tailored odorants of specific properties:
We offer the world's largest comprehensive range of odorants for gases and associated local services for natural gas (THT, Spotleak®), LPG (ethylmercaptan, Vigileak®) and industrial gases including exhaust gases in the steel industry and inert gases (Codetect®, etc.)- Natural gas & Bio-methane
- THT (TetraHydrothiophene)
- Spotleak® product line has a wide range of blends based on TBM, custom tailored mixed with IPM, NPM, MES, DMS, and THT
- Propane, Butane, LPG
- Industrial gas
Specific parameters to consider:
Each process having its own constraints, it is of utmost importance to review all process conditions and risks associated with gas leakage to perform the odorant selection according to:
- Chemical stability
- Minimize sulfur content
- Industrial context
Other parameters such as the type of injection technology used, possibility to use inert gas or odorant blanketing or even climate parameters can be taken into account in the appropriate selection of the odorant.
Odorization global logistics
Proposing customers the most appropriate odorant delivery option is the key because of the complexity and time constraints of the operation. In North America, Arkema owns and operates a full fleet of trucks for highly flexible delivery: from bulk tankers down to micro bulk trucks for “Milk Man” deliveries.
Odorization is a complex logistic process that requires long distance shipping from Europe to Americas and Asia. Arkema promotes using returnable packaging via its network of decanting and storage facilities. For example, we deliver the odorants in bulk ISO containers first, where we offload it in order to fill SBC packaging. This allows so serve the customer with shorter lead times and optimized returnable packaging rotation.
Odorflex®, your one-stop shop for odorization
- Accurate selection of the right odorant
- Assistance to odorant sampling and analysis
- Odorant handling training, from basic information about odorization to spill drills
- Technical recommendations for new installations
- On site operations for sampling, repacking, redistribution, odor control
- Odorflex® OED: odorant equipment decommissioning or cleaning before inspection
- Odorflex® EOT, equipment odorant transfer.
Odorflex® supports solutions towards the energy transition
Carbon capture and storage aim at capturing, transporting and permanently storing CO2 that would be otherwise emitted into the atmosphere. CCS technologies offer significant strategic value in the transition to low carbon economy by reducing carbon footprint of industrial activities and enabling the development of low carbon hydrogen as new energy vector.
Indeed, we are also particularly interested in the "blue" hydrogen market development, where the CO2 emitted during hydrogen production is captured and stored to reduce its carbon impact. We are therefore looking to adapt our odorant solutions for this CO2 in order to detect leakages during onshore transport but distinguishing it from natural gas.