Arkema will showcase a wide range of solutions and technologies in support of its customers’ strong commitment to decarbonization, more circularity and other sustainability goals at the 2024 American Coatings Show, April 30-May 2, in Indianapolis, Indiana (Booth # 1130).
"We will focus on three key areas at this year’s show. The first is to accelerate the development of more sustainable solutions to meet customer expectations for efficient building and indoor well-being. This includes health, protection, durability, cooler buildings along with user-friendly application with minimal environmental impact. The second is performance - supporting the industry to adopt more sustainable solutions with performance levels better than those they use today. And the last is partnership - true change will require input and collaboration from companies across the coatings value chain," said Eric Kaiser, a US regional business president for Coatings at Arkema.
Throughout the show, Arkema will showcase a wide range of sustainability related initiatives, most recently including:
Renewable-based and lower carbon footprint materials
- Bio-based segregated solutions, including UV-LED-EB-curable resins, waterborne resins and additives, featuring up to 97% bio-content.
- Bio-Mass balance solutions: Arkema is pursuing ISCC+ certification at its acrylic production
sites in North America – to complement efforts in other geographies – as part of the ambition to expand its bio-attributed mass balance resins and additives progressively worldwide for all major coating technologies including UV/LED/EB, waterborne, high solid and powders.
- Recycled-based solutions, including accelerated development of rPET-based materials, with up to 40% recycled content, for powder coating applications.
Decarbonizing the built environment
-
Lower energy intensive solutions, with new offerings for UV/EB coil coatings that offer up to 60% energy savings* during application, as well as powder resins enabling low to ultra low-temperature (as low as 135°C) cure coating applications.
*ECCA - Zero Carbon Coil Coating Line – The Way Forward
Enhancing new mobility efficiency
-
Solvent-free and lower energy intensive coating solutions for protecting battery cells, including UV/LED specialty materials for improved electrical insulation, powder resins for intumescent fire-retardant coatings and waterborne resins for liquid applied sound deadeners (LASDs).
Reducing energy consumption of buildings
-
Improved solutions for cool surface coatings, including resins and additives that enable up to 30% savings in air conditioning and ultra-durable material for building facades designed to extend the lifespan of coatings, reduce costs and improve carbon footprint.
-
Improved building efficiency with Molecular Sieves for insulated glass flexible spacers that can improve energy savings by 95% vs. non-insulated glass.
Supporting community health and well-being
- Solutions for living comfort, including resins, additives and systems designed to improve safety and provide high performance across a wide range of coating and related applications, including new low migration UV/LED curable systems for packaging inks and coatings and waterborne isocyanate-free systems for 2K industrial applications.
CONFERENCE PROGRAM
FOCUS ON SUSTAINABLE TECHNOLOGY LEADERSHIP
LOW-VOC, SOLVENT-FREE RESIN DEVELOPMENT FOR UV/EB CURED COIL COATINGS
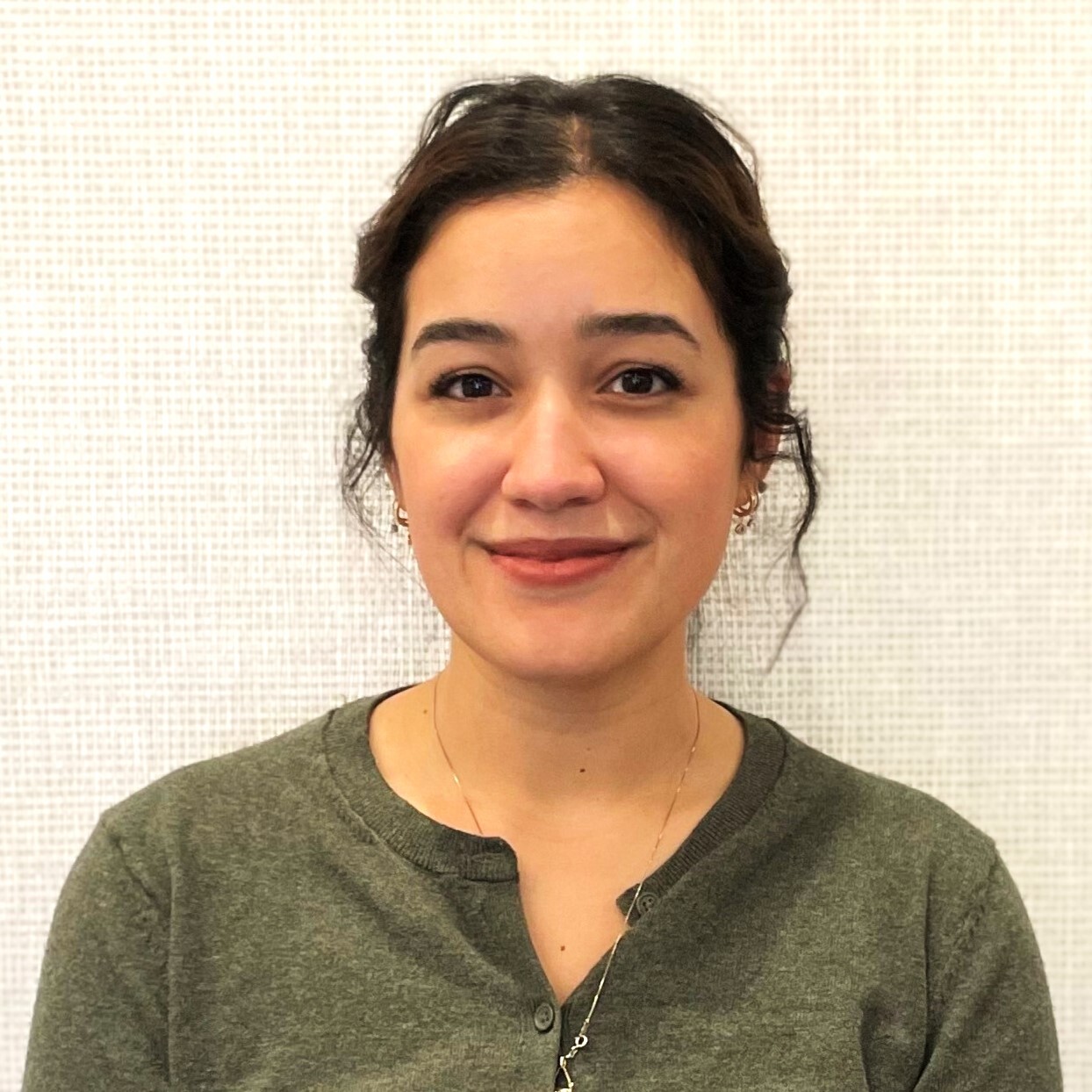
ADVANCES IN 1K PVDF/ACRYLIC HYBRID DISPERSION AND ITS APPLICATIONS
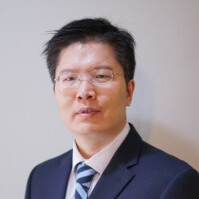
IMPROVING THE SUSTAINABILITY OF HIGH-PERFORMANCE WATER-BASED DTM COATINGS
In this paper, the current state of market for water-based direct-to-metal (DTM) coatings will be discussed. Coating end-use performance and the environmental profile of commercial DTM acrylic paints for metal will be reviewed. Gaps in end-use performance and sustainability attributes vs market needs will be discussed with an emphasis on corrosion protection, multi-substrate adhesion, block resistance, and the removal of materials of concern, including PFAS, from water-based DTM acrylic coatings. A novel technology development towards closing the performance gaps and sustainability needs of this market segment will be reviewed.
.jpg)
BUILDING PERFORMANCE EXTERIOR ACRYLICS TO MASTER REGULATORY CHALLENGES
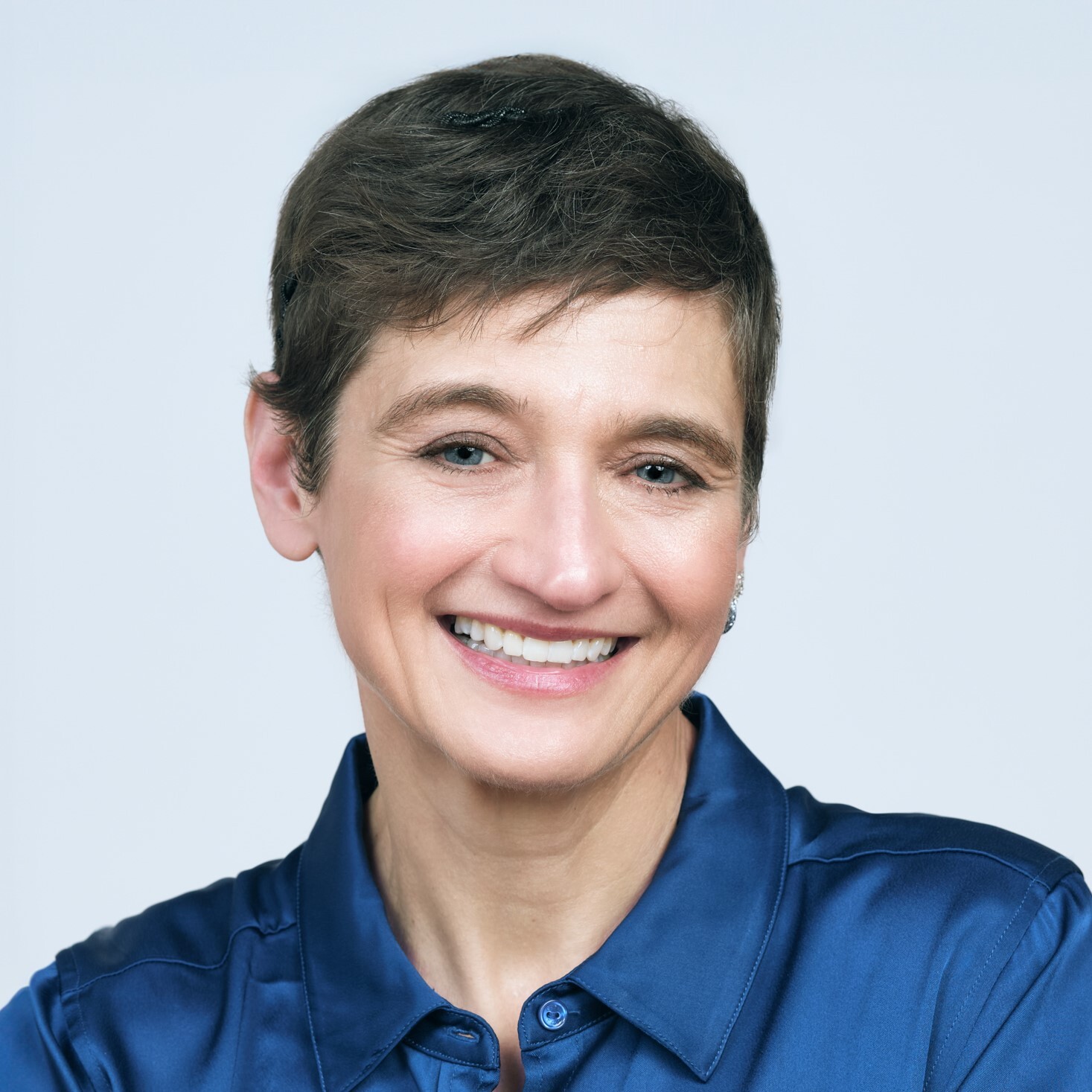
ENERGY-CURABLE SOLUTIONS FOR LOW-VOC DIELECTRIC EV-BATTERY COATINGS
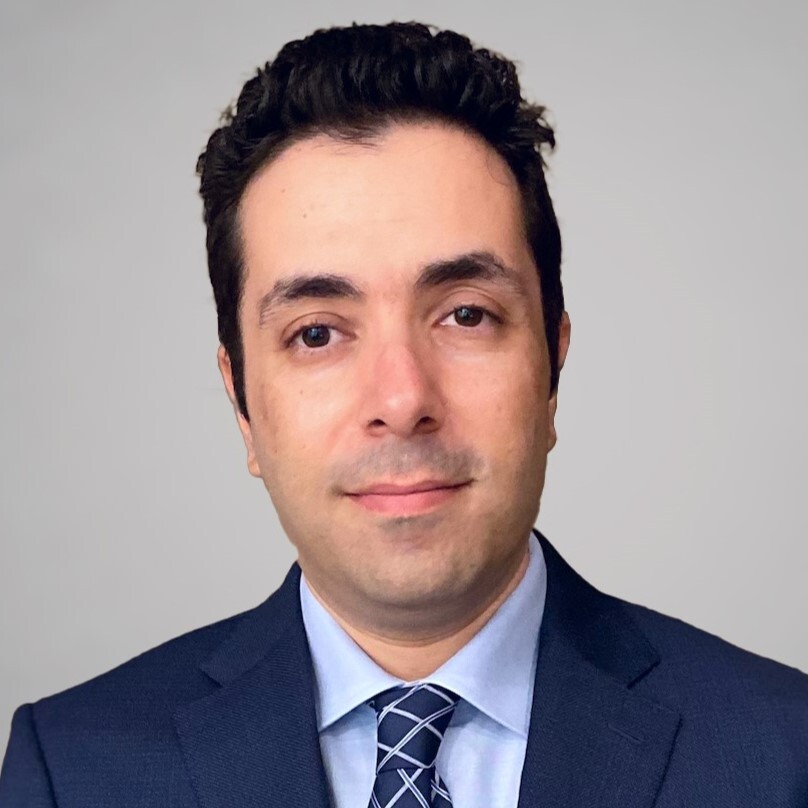
PRODUCT SPOTLIGHTS
FLAGSHIP COATING SOLUTIONS TO ADVANCE SUSTAINABILITY
.copy.png)
ENHANCING YOUR BUILDING'S SUSTAINABILITY PROFILE WITH LONG LIFE COATINGS
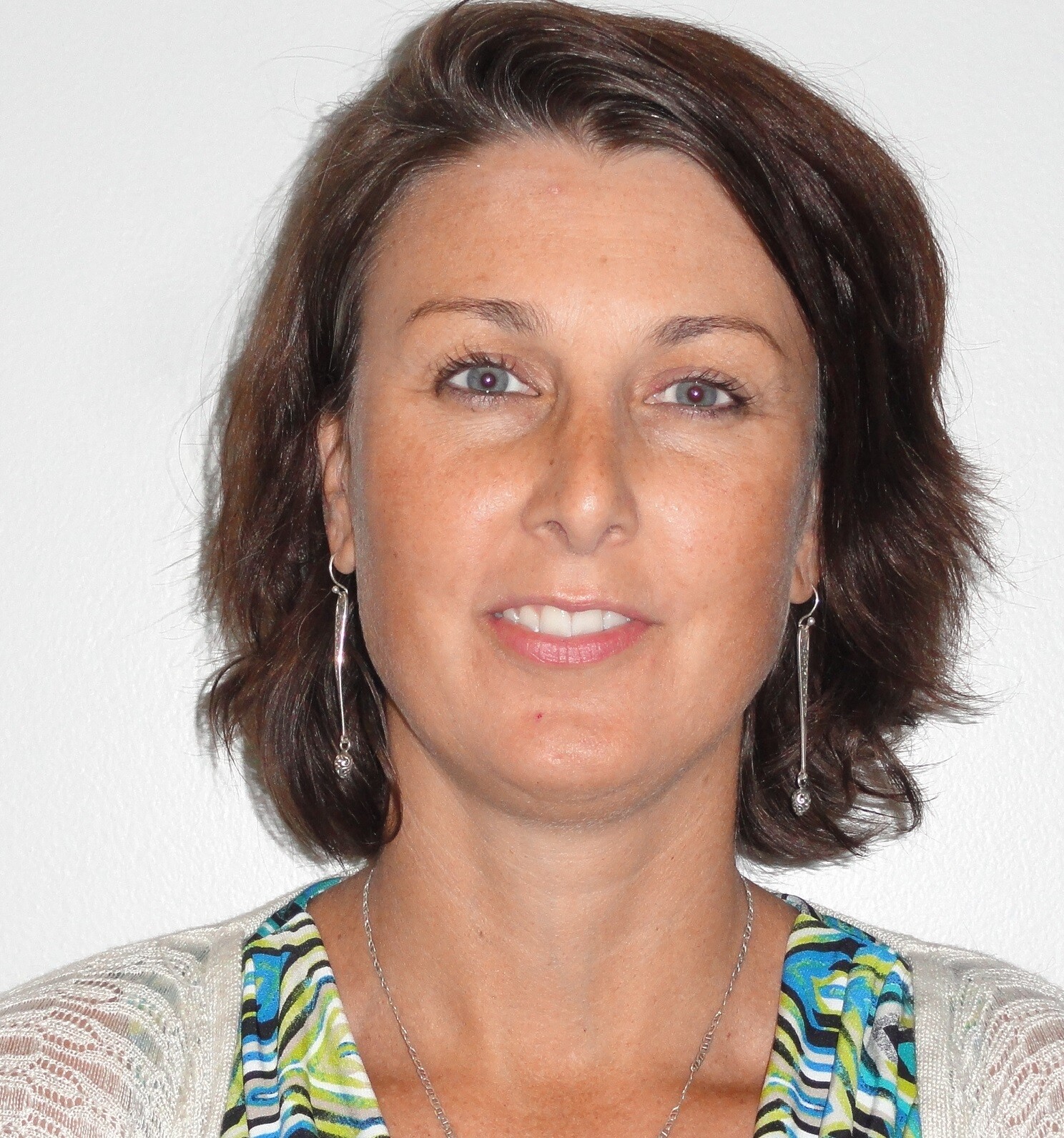
MASS BALANCE SOLUTIONS TO ACCELERATE THE SHIFT TOWARD MORE CIRCULAR SOLUTIONS
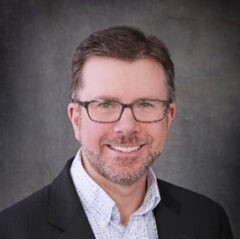
PATH FORWARD TO SAFER 2K PAINTS
NEW PURE ASSOCIATIVE & NEWTONIAN HEUR POLYURETHANE THICKENER FOR WATER-BASED SYSTEMS
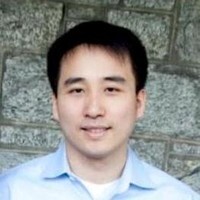